|
Tools from RR-Rail
Jock Dempsey
anvilfire guru
March 29, 2000
(Update 2011)
|
-guru |
This demo is on making tools out of RR-rail. Most of this
is stuff for the beginner or the scrounger. There may be some ideas for the rest of you.
Modern Rail road rail is a medium to high carbon steel (aprox 1075).
Pre 1860's rail is lower quality and some is actually wrought iron.
|
-guru |
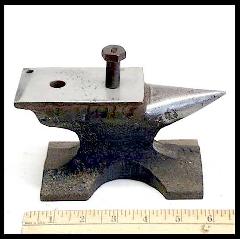 |
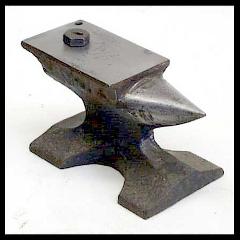 |
-guru |
This little 6" anvil is made from some old pre 1865
steel. It has a spring steel top plate welded on. The bushing that fits the round hardy
hole is made from a 1/2" bolt. It has a through hole and impression to support a #6
Capewell nail for putting initials on the faces of the head.
The entire anvil's purpose was for making horse shoe nail rings.
In general RR rail makes a lousy anvil. We will get into that latter.
|
|
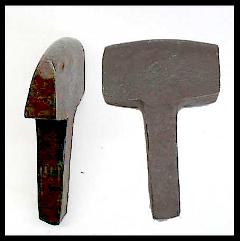 |
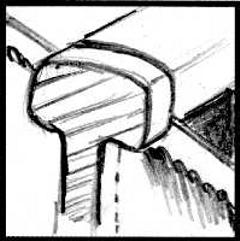 |
|
|
An Anvil Fuller |
-guru |
Heavy rail has about a 3/4" web and is great for the beginner making anvil tools to fit a small anvil (100 to 150 pounds).
This fuller was sawn off the end of a piece of 140# rail.
Note that rail is measured in the pounds per yard, not per foot like structural steel.
So a one foot piece of 140 pound rail weighs 46.7 pounds.
A one foot piece of more common 120 pound rail weighs 40 pounds and when cut to "anvil" shape maybe as little as 30 pounds.
|
|
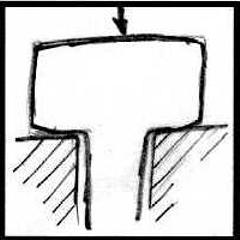 |
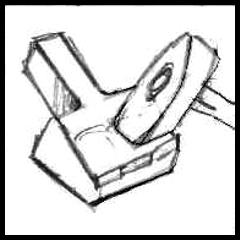 |
|
-guru |
Very little forging is required to make a fuller from rail.
A little tapering and dressing of the corners, then grind or file smooth.
For more about fullers and fullering see
Fullers and Fullering I and II
Rail is just high enough carbon that if water quenched while overheated it will crack. So I oil quench tools made from rail. |
|
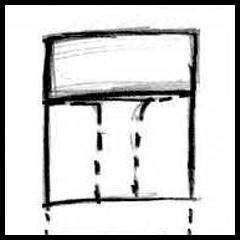 |
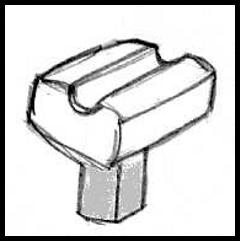 |
|
|
An Anvil Swage |
-guru |
Other anvil tools can be sawn or torch cut very close to shape.
After shaping the rough tool it can be heated an a bar or shape sunk into it.
Such tools can be flat with sharper corners than the anvil, or dressed to a dome or radius shape.
Anvil tools do many of the jobs of a swage block with less expense.
|
|
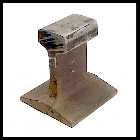 |
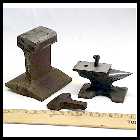 |
After cutting two fullers off the opposite ends of a short piece of rail I had a handy bench anvil.
Notice the difference in the rail sizes. |
|
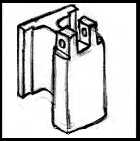 |
Rail can make a relatively low cost power hammer ram. The steel is hard enough not to need a separate die.
However, the tapered flange must be machined or ground parallel to the back.
|
|
|
|
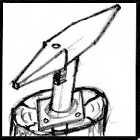 |
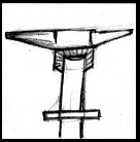 |
The carbon steel in rail is excellent for making stakes.
Here a stake is made out of the top section and welded to a piece of mild steel shafting. |
|
Earlier I said that rail makes a lousy anvil. Any of you that have tried it know that it is very springy and the curved face can take a LOT of work to dress.
The springiness is due to the designed in flexibility of the rail.
|
|
|
The Original Axial RR-Rail Anvil
If you turn a piece on end and weld it to a flange it is easy to get 9 to 12 inches of rigid MASS under your hammer.
This is such an efficient design that since describing this style anvil years ago many bladesmiths have started using anvils made form 3" to 6" diameter piece of steel shafting.
|
|
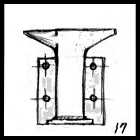 |
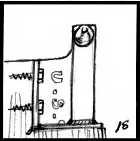 |
With a little welding and grinding that small target can be improved.
A small anvil built this way gives you the kind of rigidity you expect from a 100 pound or more anvil at 1/5 the weight.
|
|
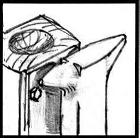 |
This final image is a little armorer's anvil with a dishing bowl carved into the stump.
A handy combination setup.
One caution when working with rail.
Used rail often has cracks and almost always has cold shuts where the surface has been extruded over the original surface from years and years of heavy freight rolling of the rail.
|
-guru |
For more RR-rail anvils and tools see
Making RR-Rail Anvils and
Gallery of Railroad Rail Anvils
|
|
|
|
|
-guru |
Any questions, suggestions or comments?
|
SmithingScout |
Can you make a hardie like you did the fuller?
|
-guru |
Yes, it would be a very similar process, just more forging.
You would want to upset the base a little more or start with a slightly thicker cut and draw the shank down a little.
The steel will harden plenty well for a hardy.
|
Ten-Hammers |
You mill the anvil face, or grind Guru?
|
-guru |
Grind it with an angle grinder and or a belt sander.
|
dimag |
Should you anneal the rail surface before attempting to cut it Jock, will it be work hardened from the wheels of the train?
|
Jim-C |
Can rail be cut in a band saw?
|
-guru |
I cut mine with a band saw with a good quality blade and had no problem.
Unless you did a first class job heating the piece to anneal it you would be likely to make it worse.
|
SmithinScout |
How would you cut the groove on the swage block?
|
-guru |
Scout, you heat up the swage, drop it in the hardy hole and pound a piece of round bar into it.
You can make round, square, or special cross sections this way.
|
Leah |
Guru, what kind of oil do you use for a quench? Do you use warm oil?
|
-guru |
I prefer either vegatable oil or clear mineral oil.
Warming is recommended but is not always done.
See our quenchants FAQ.
|
SmithinScout |
When making a small anvil like the first example, would the curve of the rail allow a groove to fill with weld to weld a top plate onto the top of the rail?
|
-guru |
Scout its alsmost impossible to weld all the way accros. This was a little light duty wire bending anvil.
|
SmithinScout |
OK, Yeah it would be a lot of welding hehe kind of impractical.
|
ironman213 |
guru, while your talking about railroad track,
I've seen it welded on the tracks before and I heard they use a thermite substance to weld it, would this work for welding large pieces or cutting them around the forge?
|
-guru |
Thermite was used extensively by the rail roads but it was also used in foundries for repairing large castings.
Thermite is only good for welding, not cutting (expept in military demolition which is not looking for clean or controlled results).
For details of Thermit rail welding see SOFA 2008 News
|
Steve-C |
Guru do you know how you identify the difference between the different years (carbon) content by sight?
|
-guru |
No. I would have to spark test or try to harden a piece.
The old wrought iron rail I have is easy to tell.
Looks like a piece of wood and torches like a stack of rusted plate.
|
Bill-Epps |
Jock I have made sevrel small anvils from switch track (7in tall) that came out real good ended up about 40 lbs with 1/2 sq. hardy hole
|
Links: |
|
iForge
is an Andrew Hooper Production
Copyright © 2000 - 2011 Jock Dempsey
HTML Copyright ©
2011 Jock Dempsey, www.anvilfire.com
Webmaster email: webmaster at anvilfire.com
|
Tools from
Jock DempseyRR-Rail
anvilfire guru
March 29, 2000
(Update 2011)
Modern Rail road rail is a medium to high carbon steel (aprox 1075). Pre 1860's rail is lower quality and some is actually wrought iron.
The entire anvil's purpose was for making horse shoe nail rings. In general RR rail makes a lousy anvil. We will get into that latter.
Note that rail is measured in the pounds per yard, not per foot like structural steel. So a one foot piece of 140 pound rail weighs 46.7 pounds. A one foot piece of more common 120 pound rail weighs 40 pounds and when cut to "anvil" shape maybe as little as 30 pounds.
For more about fullers and fullering see Fullers and Fullering I and II
Rail is just high enough carbon that if water quenched while overheated it will crack. So I oil quench tools made from rail.
After shaping the rough tool it can be heated an a bar or shape sunk into it. Such tools can be flat with sharper corners than the anvil, or dressed to a dome or radius shape. Anvil tools do many of the jobs of a swage block with less expense.
Notice the difference in the rail sizes.
This is such an efficient design that since describing this style anvil years ago many bladesmiths have started using anvils made form 3" to 6" diameter piece of steel shafting.
One caution when working with rail. Used rail often has cracks and almost always has cold shuts where the surface has been extruded over the original surface from years and years of heavy freight rolling of the rail.
For details of Thermit rail welding see SOFA 2008 News
iForge is an Andrew Hooper Production
Copyright © 2000 - 2011 Jock Dempsey
HTML Copyright © 2011 Jock Dempsey, www.anvilfire.com
Webmaster email: webmaster at anvilfire.com