|
|
|
|
|
|
|
|
|
|
|
|
|
|
|
|
|
|
|
|
|
Tell them you found it on anvilfire.com!
Blacksmithing and metalworking questions answered.
|
metal work, blacksmithing, steel, iron, forge, how-to
|
|
Rosettes or Escutcheons : Decorative Washers
Part I Tooling
Article by Jock Dempsey - anvilfire.com May 20, 2011
Fancy heavy washers or plates range from simple decorative trim to the familiar cast iron star plates used on old brick buildings.
Rosettes are often functional, acting as heavy load distributing washers.
They can also be decorative or both decorative and functional.
They can come in many styles and may be used alone, under bolts or rivets. They are particularly useful on bolts holding forged hinges.
The making of most hand forged items requires some sort of specialized tools.
Rosettes are difficult to handle and will not hold still on the anvil while being worked.
So some type of hold down is required.
The tool to the right is designed to be used on a common English anvil with hardy and pritchell hole.
The plate is required to support the positioning pin.
In a variation of this tool designed to use in a vise the plate would also provide a place to anchor the clamp.
The clamp shown hear is a simple hold-fast or bent dog such as used in many trades.
If can be made of mild or spring steel.
On a small anvil with small hardy hole spring steel is recommended.
The clamp could also be a Vise-Grip style as shown below.
Like making animal heads or faces where special
eye, nose and mouth punches are required,
it is the same making decorative rosettes.
Job preparation requires making these in advance of starting.
Often this is an R&D job but the initial punches need to be made before the first samples.
If they do not produce the desired results they can be modified or more punches made.
Almost every shape is handy to have in a variety of sizes.
Making punches for this type work are similar to
making repousse' punches as they are similar in shape and design.
Besides specialized punches common tools such as a pointed center punch and cold chisel can be used.
The easiest way to make these punches is to rework cold chisels and drift punches.
I can never find enough of these at flea markets to rework.
Related Article Links:
|
Part II Methods
Blanks for rosettes can be made using various techniques.
Thin rosettes can be punched, chiseled or flame cut.
Heavy rosettes that double as load distribution washers need to be saw cut from flat, round or square bar depending on the design.
Methods depend somewhat upon the quantity of parts being made.
In large numbers it may pay to have blanks cut by laser.
It pays to drill the center holes before slabbing the blanks off a solid OR flat bar.
In solid bar there is great saving in pre-drilling a deep hole as this is a one-time operation for many parts.
On flat bar pre-drilling the holes may be easier when handling one long piece rather than a bunch of small pieces.
Holes should be drilled oversize by 1/64" up to 1/2" and 1/32" on larger sizes.
Holes may want to be hot punched square to fit square shank bolts such as carriage bolts or custom made bolts.
Holes may also be countersunk for flat head or socket head screws.
Blanks can also be made by other less obvious methods.
A "log" can be forged or machined with the desired cross section then the blanks slabbed off.
Before using this method one should test the blank profile.
The square section shown could be creased and fullered under a power hammer, or it could be machined using a shaper of milling machine.
One log could produce from one to three dozen blanks depending on its length and the blank thickness.
"Cookies" can also be forged from common round stock under a power hammer.
Upsetting then flattening can be used to form nice thick round blanks but they can also be upset into square, round or specialized forms.
With the right sized power hammer or press this can be more efficient than many other methods.
Ogee washers and conical profiles can be produced this way.
The form can have a hole punch that nearly completes the hole.
This will help conserve and spread the metal while reducing steps.
Upsetting in a die can be medium to high quantity production method and produce blanks or finished parts.
After making the blanks the rosette is shaped into a geometric, floral, animal or human form.
As an escutcheon the design could be that of a gargoyle, panther or scull. . .
Here we are discussing geometric and floral forms.
A single tear drop shape punch can be used to make the round floral rosette at the far left.
This is a repetitive operation that can be done by hand or under a treadle hammer or
flypress.
Square blanks can be formed to shape entirely by punching and hammering or forging.
The profile can be left nearly square or worked to a four cornered star shape by hand and then punched or decorated as desired.
From round, square or triangular blanks profiles can be hand sawed with a hacksaw and dressed by filing or grinding prior to forging.
This is fairly efficient in small quantities. If large quantities are needed then machine flame cutting is recommended.
To finish the shape at left a triangular or diamond shaped set down punch is used between the petals.
Then either a pair of right and left hand airfoil or tear drop shapes is used to swage the petals OR a series of general punches could be used in combination.
A similar or more acutely shaped blank can have each petal drawn out.
These can then be scrolled upward or curved to the side making multiple "S" shapes to give a spiral effect
to look like a turbine, windmill or octopus.
Thick and thin triangular or other shape blanks can be shaped then stacked.
Stacked rosettes of different sizes and shapes can produce wonderfully complex textures with a lot of depth.
Two triangles one set down and one up, mounted offset can create a lot of depth and interest without a great deal of work.
Thinner material such as the 1/8" (6mm) plate is relatively easy to plasma cut cleanly by hand into various shapes.
When you stack up four pieces of 1/8" material that is 1/2" in the center.
Display Pieces (right) - Michael Walker was showing off these interesting display pieces at Dan Boon's February 2000.
They are assembled with the center stud and a spring clip so that they can be taken apart. Approximately 4 to 5" (100 to 125mm).
Each Estucheon is made from multiple pieces that would be held together permanently by the center stud that passes through a gate or door.
Except for the center stud these are made from 1/8" plate that is cut and forged.
Stacked up they give the impression of great mass and complexity.
You can see in Michael's work that he has used a variety of punches.
The large rounds are probably done with a struck ball pein hammer with the work supported over a
pipe, wood block or swage block.
This kind of work can be done both hot and cold but in the thickness material that goes with forge work (1/8" and over) it is best done hot.
Related Article Links:
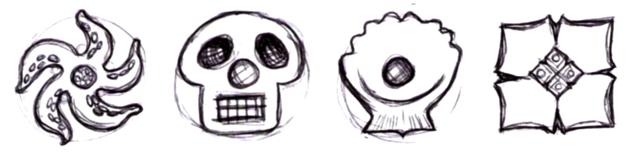
Octopus, Scull, Shell and Perl, Blocks
|
Copyright
©
2011 Jock Dempsey, www.anvilfire.com
Webmaster email: webmaster at anvilfire.com
|
|
|
Rosettes or Escutcheons : Decorative Washers
Part I Tooling
Article by Jock Dempsey - anvilfire.com May 20, 2011
Fancy heavy washers or plates range from simple decorative trim to the familiar cast iron star plates used on old brick buildings. Rosettes are often functional, acting as heavy load distributing washers. They can also be decorative or both decorative and functional. They can come in many styles and may be used alone, under bolts or rivets. They are particularly useful on bolts holding forged hinges.The tool to the right is designed to be used on a common English anvil with hardy and pritchell hole.
The plate is required to support the positioning pin. In a variation of this tool designed to use in a vise the plate would also provide a place to anchor the clamp.
The clamp shown hear is a simple hold-fast or bent dog such as used in many trades. If can be made of mild or spring steel. On a small anvil with small hardy hole spring steel is recommended.
The clamp could also be a Vise-Grip style as shown below.
Like making animal heads or faces where special eye, nose and mouth punches are required, it is the same making decorative rosettes. Job preparation requires making these in advance of starting. Often this is an R&D job but the initial punches need to be made before the first samples. If they do not produce the desired results they can be modified or more punches made. Almost every shape is handy to have in a variety of sizes.
Making punches for this type work are similar to making repousse' punches as they are similar in shape and design. Besides specialized punches common tools such as a pointed center punch and cold chisel can be used.
The easiest way to make these punches is to rework cold chisels and drift punches. I can never find enough of these at flea markets to rework.
Related Article Links:
Part II Methods
Blanks for rosettes can be made using various techniques. Thin rosettes can be punched, chiseled or flame cut. Heavy rosettes that double as load distribution washers need to be saw cut from flat, round or square bar depending on the design.
Methods depend somewhat upon the quantity of parts being made. In large numbers it may pay to have blanks cut by laser.
It pays to drill the center holes before slabbing the blanks off a solid OR flat bar. In solid bar there is great saving in pre-drilling a deep hole as this is a one-time operation for many parts. On flat bar pre-drilling the holes may be easier when handling one long piece rather than a bunch of small pieces.
Holes should be drilled oversize by 1/64" up to 1/2" and 1/32" on larger sizes. Holes may want to be hot punched square to fit square shank bolts such as carriage bolts or custom made bolts. Holes may also be countersunk for flat head or socket head screws.
Blanks can also be made by other less obvious methods. A "log" can be forged or machined with the desired cross section then the blanks slabbed off. Before using this method one should test the blank profile. The square section shown could be creased and fullered under a power hammer, or it could be machined using a shaper of milling machine. One log could produce from one to three dozen blanks depending on its length and the blank thickness.
"Cookies" can also be forged from common round stock under a power hammer. Upsetting then flattening can be used to form nice thick round blanks but they can also be upset into square, round or specialized forms. With the right sized power hammer or press this can be more efficient than many other methods. Ogee washers and conical profiles can be produced this way. The form can have a hole punch that nearly completes the hole. This will help conserve and spread the metal while reducing steps.
Upsetting in a die can be medium to high quantity production method and produce blanks or finished parts.
A single tear drop shape punch can be used to make the round floral rosette at the far left. This is a repetitive operation that can be done by hand or under a treadle hammer or flypress.
Square blanks can be formed to shape entirely by punching and hammering or forging. The profile can be left nearly square or worked to a four cornered star shape by hand and then punched or decorated as desired.
From round, square or triangular blanks profiles can be hand sawed with a hacksaw and dressed by filing or grinding prior to forging. This is fairly efficient in small quantities. If large quantities are needed then machine flame cutting is recommended.
To finish the shape at left a triangular or diamond shaped set down punch is used between the petals. Then either a pair of right and left hand airfoil or tear drop shapes is used to swage the petals OR a series of general punches could be used in combination.
A similar or more acutely shaped blank can have each petal drawn out. These can then be scrolled upward or curved to the side making multiple "S" shapes to give a spiral effect to look like a turbine, windmill or octopus.
Thick and thin triangular or other shape blanks can be shaped then stacked. Stacked rosettes of different sizes and shapes can produce wonderfully complex textures with a lot of depth. Two triangles one set down and one up, mounted offset can create a lot of depth and interest without a great deal of work.
Thinner material such as the 1/8" (6mm) plate is relatively easy to plasma cut cleanly by hand into various shapes. When you stack up four pieces of 1/8" material that is 1/2" in the center.
Each Estucheon is made from multiple pieces that would be held together permanently by the center stud that passes through a gate or door. Except for the center stud these are made from 1/8" plate that is cut and forged. Stacked up they give the impression of great mass and complexity.
You can see in Michael's work that he has used a variety of punches. The large rounds are probably done with a struck ball pein hammer with the work supported over a pipe, wood block or swage block. This kind of work can be done both hot and cold but in the thickness material that goes with forge work (1/8" and over) it is best done hot.
Related Article Links:
Octopus, Scull, Shell and Perl, Blocks
Copyright © 2011 Jock Dempsey, www.anvilfire.com
Webmaster email: webmaster at anvilfire.com