J-J :
01:43:11 |
Tonight's demo is on what I use in lieu of a swage block.
Someday, I hope a real blacksmith designs a swage block for us instead of a foundry, until
then, ...there's what many of us do... |
J-J :
01:43:56 |
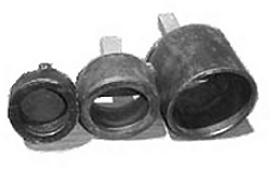
|
J-J :
01:44:40 |
These cups are 2", 3" and 4" dia. bearing races
I got at the secondary scrap yard.... |
J-J :
01:45:11 |
I gas cut a plate to fit the bottom, welded it in place, then
welded a hardy shank on. |
J-J :
01:46:03 |
I use these and several other sizes for most of the cups and
bowls I make. Last month I made 120 5" dia candle cups in less than a day on the
3" cup. |
J-J :
01:47:23 |
The thing to remember is we are using the round perimeter for
an anvil base and our hammer on top to form a rounded shape. We don't need a solid bottom,
just move it around a bit with the tongs as you hammer the cup. |
J-J :
01:47:57 |
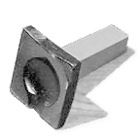
|
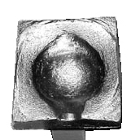
|
J-J :
01:49:42 |
This is a soup spoon mold or swage, I made using the 2"
dia cup swage I showed last, and a rounding hammer struck with a 3# copper hammer, to form
the spoon swage. |
J-J :
01:50:34 |
I then took the spoon plate to the post vice and shaped the
tip and handle recess with a Dremel tool and small cutoff wheel. |
J-J :
01:51:20 |
Then I welded a hardy shank to the bottom. Works great. Here's
another way I make spoons... |
J-J :
01:51:36 |
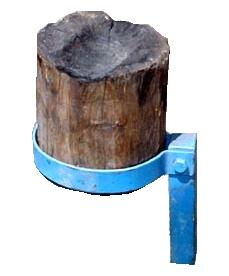
|
J-J :
01:52:32 |
This is a 6" dia tree limb with 113 growth rings, so it's
pretty dense. |
J-J :
01:53:35 |
I drilled the hardy shank for a bolt, and wrapped a 1" x
1/8" mild steel strap around the stump and tightened it up firm. It, of course, rests
on the anvil and is very solid. |
J-J :
01:54:40 |
Don't try grinding or burning out any wood for making a spoon.
The heat from your working stock will be beaten down into the wood as you hammer it
(believe it or not :) ). |
J-J :
01:55:45 |
Eventually, the spoon hole will get burned larger than will be
effective for small dinner spoons. That's when you begin using that hole for serving
spoons. Switch ends and start over for dinner spoons. |
J-J :
01:56:25 |
Also, it won't hurt to soak the wood block in water for a few
hours prior to use, with about an hour of drying out before you use it. |
J-J :
01:57:27 |
For ladles, if I'm in a hurry, I'll take a 4" grinder
with a chain saw head from harbor freight and rough in the ladle shape and get to it. |
J-J :
01:58:35 |
For relatively light weight stock, say 16 ga and less, I have
a sleeve from an old welding jacket filled with lead shot and sewn closed. I work the
steel cold using the bag as a soft anvil. |
J-J :
01:58:49 |
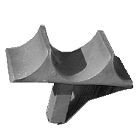
|
J-J :
01:59:29 |
For general bending of an inside diameter shape, I use this
tool a lot. |
J-J :
02:00:36 |
It is a section of driver for a crawler tractor, and I place
the bar (for instance) over the two bumps, and strike down near the center. I rotate the
stock as necessary and it is fast and effective. |
J-J :
02:01:17 |
One full time, long-time smith I know, uses two parallel
sections of railroad track welded to a heavy plate to achieve the same effect. |
J-J :
02:02:06 |
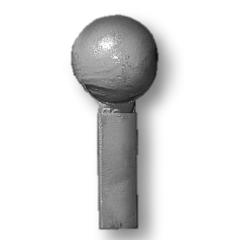
|
J-J :
02:02:51 |
Sometimes you need to make a small concave shape and having
balls of different sizes welded to hardy shanks is just the ticket. |
J-J :
02:03:54 |
This one is a 2" trailer hitch ball, but cast iron balls
are often found in large sizes 5" dia and up, and can be welded to the hardy shank
with hi-nickle welding rod. I use these quite often. |
J-J :
02:04:07 |
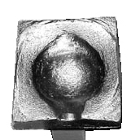
|
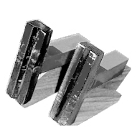
|
J-J :
02:05:16 |
Please excuse my photography and thank Guru for a remarkable
effort in this pic.... |
J-J :
02:06:04 |
The top piece is 1" sq. stock of mild steel, or 4140. I
made a series of these in v and half round.... |
J-J :
02:07:10 |
I forge these after welding them together. I heat the top
yellow hot, drop into the hardy hole and lay a piece of round stock over the bar and drive
it in half way. |
J-J :
02:08:01 |
I use 1`/4", 3/8", 1/2" 5/8", 3/4" in
the 1" sq. stock, and then go to larger stock for larger sizes. |
J-J :
02:09:05 |
After forging the weld will be shot. Separate the 2 pieces,
grind smooth again and reweld. |
J-J :
02:10:08 |
For the v-shape, I make the v's with a 1" sq. stock, with
one sharp corner ground flat for a hammering surface. I use an old "beater"
hammer of 4# to drive the v into the swage material. |
J-J :
02:11:03 |
These are the primary tools I use on a daily basis in the shop
in lieu of a swage block. |
J-J :
02:11:03 |
Questions
and comments? |
Leah :
02:12:08 |
J-J, what kind of wood is the tree limb? |
Fred :
02:12:41 |
J-J , Although I've used bearing races myself, I've always
been concerned they are tempered to such a hardness that they may be brittle and shatter
without annealing them/ input all? |
Jim-C :
02:12:44 |
Would you explain again how the first ones (bearing) cups are
used? |
Barne :
02:12:54 |
These look easier to move around the shop than the big swage
blocks |
J-J :
02:13:00 |
Redwood. A very soft outer wood but very hard tight grain on
the heart wood. |
Tapley :
02:13:20 |
Hats off to ingenuity and the desire to share info J-J,
thanks. |
Tedd-Harris :
02:13:44 |
Yes, anneal the bearing races first, heat treat again later,
if you want. |
Jock-D :
02:14:02 |
Great job JJ. Of course you know someone will be selling these
on eBay next week! Fred I would use pipe or pipe couplings from the tubular sections. |
Steve-C :
02:15:01 |
J J could you use some pipe and just for the tool that you
made for a crawler parts? |
Leah :
02:15:07 |
great ideas, thanks J-J, I will look at the scrap pile at work
a lot closer now |
J-J :
02:15:15 |
Jim, place the bearing cup shank in the hardy. Take a 5"
dia cutout of 1/4" stock. Heat it to orange. Hold it over the 3" cup and smack
it right in the center with a rounding hammer. Then you'll see the shape start forming
fast. Just rotate the stock in a circular pattern and continue taping with the rounding
hammer. Takes about 1 1/2 mins. to make a nice cup. |
J-J :
02:17:12 |
Yes, thanks for reminding me! Thick wall pipe sections are
great and do not need heat treating. Bearing races must be annealed, then hardened and
drawn to a levy blue before beginning the fabrication. |
Steve-C :
02:17:40 |
J J do you put a taper on the bearing races to keep them from
gouging the cups |
J-J :
02:18:06 |
Steve, I didn't understand the question about the tractor
part. |
Jim-C :
02:18:28 |
Lots of used oil field drill pipe will be close to 4130; can be
water quenched OK. |
J-J :
02:19:17 |
Steve, Daryl Nelson once told me "chamfer, chamfer,
chamfer!!!!!!!!" I don't even think about it anymore. You will be hard pressed to
find a sharp edge in my shop except on cutting tools. |
Steve-C :
02:20:38 |
I thought I could make the it out of pipe instead of using
that? |
J-J :
02:21:39 |
Let me add that if you visited 50 shops, you'll probably find
47 different ways of doing what I've shown here tonight. This is how I do cause that's the
scrap I had to work with when I needed the tool. Be inventive, and think in terms of the
capability of each tool and the extreme limits of the material being works. Henry Ford
said that in the 1920's and it was handed to me in 1965 in a steel fab shop by the owner
who had worked for Henry. |
J-J :
02:22:52 |
Steve, it would work if the pipe was good and heavy, I guess.
give it a shot./ |
Barne :
02:23:29 |
Yes JJ I agree . As long as it works.. |
Steve-C :
02:23:59 |
I could weld some plate to the sides and make it look the same
as that and it would be pretty heavy |
J-J :
02:26:41 |
Guys, another shape I use a lot and have seen in several
shops, is a large chain link (3/4" dia to 1 1/2" dia stock) welded to a hardy
shank, and used for oblong shapes. Didn't want this to be too long so didn't shoot a pic
of it. But think in terms of different shapes. |
Barne :
02:28:24 |
I have some old anchor chain. It would make a nice big bowl.. |
Tedd-Harris :
02:29:22 |
Barne: is that old anchor chain made of wrought iron? |
J-J :
02:29:47 |
Barne, Whitesavage and Lyle, artist blacksmith shop in
Seattle, uses anchor chain swages daily in making the art work that gets welded to large
fences, etc. |
Swage Tools
Demonstration by James Joyce.
May 29, 2000 (Edited May 23, 2011)
J-J :
01:43:11
J-J :
01:43:56
J-J :
01:44:40
J-J :
01:45:11
J-J :
01:46:03
J-J :
01:47:23
J-J :
01:47:57
J-J :
01:49:42
J-J :
01:50:34
J-J :
01:51:20
J-J :
01:51:36
J-J :
01:52:32
J-J :
01:53:35
J-J :
01:54:40
J-J :
01:55:45
J-J :
01:56:25
J-J :
01:57:27
J-J :
01:58:35
J-J :
01:58:49
J-J :
01:59:29
J-J :
02:00:36
J-J :
02:01:17
J-J :
02:02:06
J-J :
02:02:51
J-J :
02:03:54
J-J :
02:04:07
J-J :
02:05:16
J-J :
02:06:04
J-J :
02:07:10
J-J :
02:08:01
J-J :
02:09:05
J-J :
02:10:08
J-J :
02:11:03
J-J :
02:11:03
Questions and comments?
Leah :
02:12:08
Fred :
02:12:41
Jim-C :
02:12:44
Barne :
02:12:54
J-J :
02:13:00
Tapley :
02:13:20
Tedd-Harris :
02:13:44
Jock-D :
02:14:02
Steve-C :
02:15:01
Leah :
02:15:07
J-J :
02:15:15
J-J :
02:17:12
Steve-C :
02:17:40
J-J :
02:18:06
Jim-C :
02:18:28
J-J :
02:19:17
Steve-C :
02:20:38
J-J :
02:21:39
J-J :
02:22:52
Barne :
02:23:29
Steve-C :
02:23:59
J-J :
02:26:41
Barne :
02:28:24
Tedd-Harris :
02:29:22
J-J :
02:29:47
guru:
iForge is an Andrew Hooper Production
Copyright © 2000 James Joyce
HTML Copyright © 2000-2011 Jock Dempsey, www.anvilfire.com
Webmaster email: webmaster at anvilfire.com