|
 |
 |
 |
-GURU
|
The Peter Wright anvil on a red oak stand at top is a classic. This is a short section of log that sets on the ground and the anvil sets on top. Usually there are some spikes driven in the stump to keep the anvil from walking off from vibration.
Some smiths strap their anvils down to reduce the ring. I prefer to be able to lift mine off the stand if needed.
In old shops with permanent forge and anvil locations longer sections of logs like this were often set deep in the ground. When you do this you want to be VERY sure that you will not want to change your anvil location. Most modern smiths prefer some degree of portability.
|
 |
 |
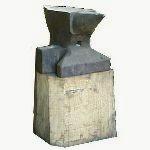
Figure 6 Click for Detail |
This old German anvil is setting on an oak stump that was trimmed to fit.
The piece of oak was collected after an ice storm. Often after wind or ice storms you can have your choice of log sections if you ask and have a way to haul them home.
Don't forget that a taller section of log is a handy stand for a swage block OR to carve depressions in the end for forming sheet metal.
|
 |
-GURU
|
But, we are not always so lucky to have windfalls of large logs available OR the chain saw to cut to size. OR have them available when we NEED a stand.
There are numerous ways to build an anvil stand. They can be wood or metal.
|
 |
 |

Figure 11 Click for Detail |
This anvil stand was built by Steve Barringer of B2 Design in Mooresville, NC.
It is a solid section built up by laminating pieces of 2x12 framing lumber.
The unique and HANDY thing about this design is the offset Steve put in the pieces as he stacked them up.
NOTE: When I was making my drawing below I had not looked at this photo for a year.
I'd forgotten that Steve's end boards were 1-1/2" taller than the others to retain the anvil.
|
 |
 |
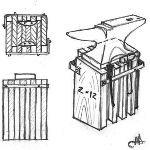
Figure 1 Click for Detail |
Each board is offset about 1-1/2 to 2" as they are stacked up.
I suggest using yellow carpenter's glue and glue coated nails.
Steve says:
If you look at the ends of the anvil stand you will notice the 1/2" threaded rods that hold the thing together.
There are no nails or shims and the anvil sits on a bed of silicone caulking (really
helps the ringing). The threaded rod actually clamps the anvil in place.
|
 |
-GURU
|
Steve attached a metal strap to make "pockets" to hold tools.
In my drawing I show how to do it if you have an even number of boards and the ends do not come out the same.
I show 8 boards, Steve used 9.
To create the right fit you may need an extra "shim" made of plywood so the stack of lumber comes out the proper dimension to fit your anvil.
The tool holding strap could also be a strip of hardwood. There are a lot of ways to adapt this design to suit yourself.
|
 |
 |
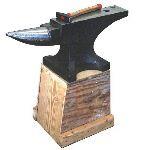
Figure 22 Click for Detail |
This is the style of stand I have been using for 28 years. When this photo was taken for a magazine I had not put the blocks on that keep the anvil in place.
This is a hollow light weight stand that is VERY solid. I can not tell it from a solid section of log in use. The hollow center also helps it sit flat on uneven surfaces. I have used these stands on all sorts of surfaces ranging from concrete to soft wet ground.
|
 |
 |
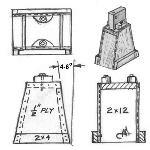
Figure 2 Click for Detail |
This stand is built from 2x10 or 2x12 (nominal construction size) lumber depending on the size anvil you have. But 2 x 12 seems to work best for most anvils. The anvil above is a 300 pound Kohlswa. It just does fit. A 200 pound anvil leaves a little space around the edges.
Two sides are 2x12 and the other two are covered with 1/2" plywood. A 2x4 reinforces and stiffens the bottom edge of the plywood. This also make the base a little larger.
|
 |
-GURU
|
The angled side is 4 to 6 degrees from square. I usually measure this as 1.5:18 or 2:18 in inches as I layout the lumber. This stand is approximately 17" tall to fit me and the large anvil. Other stands I built the same day were 18" for smaller anvils.
|
 |
-GURU
|
I glue and nail all the joints including the plywood. The plywood is also nailed to the 2x4's from the inside.
I use sheet rock nails on the plywood because they have large heads and anti-pullout ridges.
|
 |
 |

Figure 4 Click for Detail |
Many smiths also make steel stands. This photo is of a stand NOT to make.
The legs are spindly, and there are no diagonals or feet.
On stands of this sort that I have used the anvil bounced around and made clanking sounds. . .
It appears (see addendum) to be too tall for general work so
it may be a light duty stand for close detail work. But you don't want to use this on soft ground or asphalt due to the lack of feet.
It will end up embedded in either surface and leaning precariously.
|
 |
 |
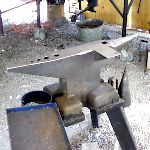
Figure 5 Click for Detail |
This is a Hoffi anvil on a steel stand. Although the legs have no diagonal bracing it is made of very heavy angle iron that is very stiff (3/8" x 4 x 4) and a piece of 1/2" steel plate.
This stand has some handy and unique features.
|
 |
-GURU
|
The base is cut to fit around the anvil feet.
This lets you use the space in between to brace a piece being upset using a swage block or floor anvil.
There is a little built in container to catch punching "biscuits" that can be filled with water to cool them as they drop out. And the other end has a rack for hardies and other anvil tools.
I am not a proponent of steel stands but this one seemed to work well.
|
 |
 |

Figure 7 Click for Detail |
A common stand in Europe is a container filled with sand or coal ashes.
The anvil sets in the fill and can be leveled or the height adjusted by giving it a twist.
With the base partially buried in sand the ring is dampened somewhat.
|
 |
-GURU
|
This type stand is VERY heavy with the fill and can be made of a cut off oil drum or a fabricated container.
The Peddinghaus stand above is a commercial rectangular box stand with handles.
I don't think the handles will do much good with 400 pounds of sand in a 75 pound box. . .
|
 |
-GURU
|
Questions, Comments?
|
 |
Pete F
|
Hoe does the hollow stand compare to solid for everyday work?
|
 |
possum
|
very informative Jock, I use blocks of cross ties, makes it easy to adjust the height if my son is using the anvil
|
 |
Leah
|
Nice demo, Jock. I really like the stand Steve Barringer made. That is a good design for a tool holder.
|
 |
-GURU
|
Pete, I cannot tell the difference. The corners of the anvil set over the heavy pieces of 2x12 that go to the ground. It is very solid.
|
 |
PF
|
efficient transmission= added mass?
|
 |
-GURU
|
Pete it may help small anvils but I have used anvils from 100 pounds to 300 pounds on these stands. I used the 100 on a solid stump and it was no different.
But it is easy to take the same amount of lumber and make a very flimsy stand.
|
 |
Ntech
|
Does the weight of the stand have any effect on the way the metal moves on the top of the anvil? Would a light stand do as well as say a 500 pound stand for the same anvil?
|
 |
PF
|
admirable design..
|
 |
-GURU
|
Unless the anvil is rigidly affixed to a solid block (machined surfaces, bolted down) the weight does not add appreciably to the efficiency. It DOES make the stand solid and not move around. The sand filled stands at 500 pounds or so are VERY solid. Add the weight of the anvil and you have a veritable immovable object. But it does not add to the anvils efficiency.
However, a springy steel stand or a flimsy wood stand that lets the anvil move around will reduce its efficiency a lot.
|
 |
-GURU
|
ADDENDUM:
From Glenn Conner, maker of the stand in Figure 4 (My DO NOT example).
That stand is 1-1/2" x 1-1/2" x 1/4" angle iron for the legs and 2x3x1/4" angle iron for the box.
It is 9x12 at the box and 18x18" at the floor.
Yes, I thought that it looked too tall also, but is about 24" at the box and 2" above knuckle high (on me) at the face.
The original plan was to put an angle iron frame 6" off the bottom and a 1/4" plate steel shelf.
Never got that far - yet. This is used outside on a creek gravel foundation and will only bury in about 1/2" at most.
The only differences I have found is that the ring of the anvil if best on wood.
The wood stump (top photo) was great till the bugs found it.
Tried everything I could think of to discourage them, but they are still there.
Both wood and angle iron are a solid base.
The hammer works just a bit better on the angle iron. The angle iron is easier to move and setup.
Angle iron will reduce the ring considerably.
(Its the mounting, not the angle iron. -GURU)
Metal to metal contact between the anvil and angle iron was a concern so I put a piece of 1/2" wood (pine) between them.
This seemed to cushion the anvil and adjust it to the stand.
No more high spots to rock, or low spots that did not contact, again an improvement.
think 1/4" or 1/8" wood would work even better. Nice imprint in the wood from the anvil last time I looked :)
Wrap it with chain, put a magnet under the heel and I have used the angle iron at 3 am without the neighbors being upset.
On wood, the same anvil (without a muffler) can be heard at 4 city blocks during the summer.
|
 |
 |
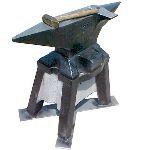
Figure 8 Click for Detail |
From Woody in Nebraska:
This anvil has a ring that will make your toes literally double over!
After setting it into the form fit stand, the ring transferred down one of the legs!
Looking back the ring could have been reduced with a magnet on the leg.
|
 |
WOODY
|
However, I'm extremely pleased with the 3 cu ft of concrete cast into the steel base which reduces the annoying ring to a pleasant dull thud.
Mounting the anvil which has a rough cast convex base was solved by placing lead wheel weights in the corners, has worked very well!
The flat iron straps transition to threaded bolts for tightening work extremely well!
My only grief about the base is that I didn't offset the perimeter ring for upsetting long corners.
Occasionally I entertain the idea of cutting the iron and welding a band underneath to replace it.
Then chiseling a groove though the cement.
Can't say enough about my enthusiasm for the concrete!
Today I bent a 3/4 bending wench on a close bend using a fork placed in the anvil, didn't move the anvil around at all.
It's not my choice to endorse this anvil (you get what you pay for, and it is a serviceable anvil at a low price!)
|
 |
 |
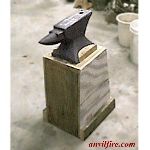
Figure 9 Click for Detail |
Rob Pierce from Ohio
Pefect timing on the Anvil Stand tutorial!!
I built this one out of 2x12's from my scrap pile with no out of pocket expense :-)
That's what I like!
Now I'm building my gas forge stand out of an old grill.
Pierce Productions
Media Project Studio
Cincinnati, Ohio
|
 |
 |
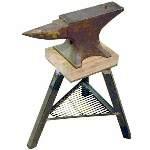
Figure 12 Click for Detail |
From Jim. C (CSI) Added October 20, 2002
This is another 3 legged stand like Woody's and the Hoffi stand by Tom Clark. This one is a little fancier.
Legs are 2 x 2 sq. tube 1/8 - 3/16" wall
Plate above legs 3/8" thick.
Wood is 2 x 12 pine with pattern sections cut and added to hold anvil.
Spikes are cut short and drilled and tapped at the bottom; bolts & washers hold spikes against the anvil.
Surrounding kick plate is 10 gage.
|
 |
 |
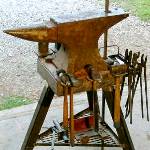
Figure 13 Click for Detail |
Legs are cut to 22° angle; the back legs are rotated 45° from centerline.
Legs are plugged at the bottom. Plug is about 1/2" up inside tube.
This stand is similar to Tom Clark's; I like it because I can work up very close to the anvil.
Note (thanks to Paw-Paw): The hardie hole is open to the ground for an upsetting plate.
|
 |
 |

Figure 14 Click for Detail |
This stand sits solid on dirt (portable / demo) or on my shop floor.
It does not ring.
I still personaly like a plain wooden stand but if you want a steel stand with tool holding capacity I really like the details of this one.
The tool rack made of stove rack or barbeque grill, the Rail Road spike hold downs, tong rack. . .
- guru
|
 |
 |
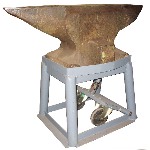
Figure 15 Click for Detail |
From Mart Salumaa of Estonia.
I use in my workshop 3 different anvils.
This one is very heavy and I do not use it every day.
It stands away in my smithy. But it is bad idea to run with red hot iron in the workshop.
For moving this 200 kg (440 lbs) anvil I made stand on the wheels with a jackscrew.
It is important to put rubber between the stand and anvil.
Best regards: Mart Salumaa www.hot.ee/theblacksmith/
|
 |
 |
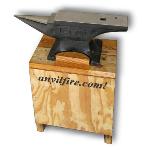
Figure 16 Click for Detail |
From product report by Robert Nichols AKA quenchcrack
Delta TFS 100 pound anvil on stand.
Stand made from framing lumnber and 1/2" plywood with D-lugs to position anvil.
|
 |
 |
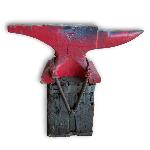
Figure 17 Click for Detail |
From Columbian Anvil in the anvil gallery.
This is a classic method of strapping an anvil down to a heavy wooden stump.
It requires long bars threaded on the ends and designed to fit.
While the stand is smaller than the base of the anvil (it should not be) this was not uncommon in industrial shops.
My large Kohlswa was attached to the end of a short section of riveted column with flanges smaller than the anvil base.
It was strapped down with bent 1/2" square bar welded to the stand.
|
 |
 |
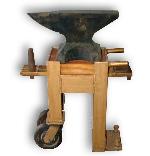
Figure 18 Click for Detail |
From Vulcan Anvil in the anvil gallery.
This is an unusual wheeled stand with tool racks and handles.
The total weight being about 300 pounds requires 150 pounds of lift on the handles.
To be really easy and convienient I would make slip on handle extensions to make this easy to roll and control.
|
 |
Click for Detail
Demonstration by Jock Dempsey
August 14, 2002, Appended 8/16, 9/7, 10/20, 2005 (updated may 28, 2011)
Some smiths strap their anvils down to reduce the ring. I prefer to be able to lift mine off the stand if needed.
In old shops with permanent forge and anvil locations longer sections of logs like this were often set deep in the ground. When you do this you want to be VERY sure that you will not want to change your anvil location. Most modern smiths prefer some degree of portability.
Figure 6
Click for Detail
The piece of oak was collected after an ice storm. Often after wind or ice storms you can have your choice of log sections if you ask and have a way to haul them home.
Don't forget that a taller section of log is a handy stand for a swage block OR to carve depressions in the end for forming sheet metal.
There are numerous ways to build an anvil stand. They can be wood or metal.
Figure 11
Click for Detail
NOTE: When I was making my drawing below I had not looked at this photo for a year. I'd forgotten that Steve's end boards were 1-1/2" taller than the others to retain the anvil.
Figure 1
Click for Detail
Steve says:
If you look at the ends of the anvil stand you will notice the 1/2" threaded rods that hold the thing together. There are no nails or shims and the anvil sits on a bed of silicone caulking (really helps the ringing). The threaded rod actually clamps the anvil in place.
The tool holding strap could also be a strip of hardwood. There are a lot of ways to adapt this design to suit yourself.
Figure 22
Click for Detail
This is a hollow light weight stand that is VERY solid. I can not tell it from a solid section of log in use. The hollow center also helps it sit flat on uneven surfaces. I have used these stands on all sorts of surfaces ranging from concrete to soft wet ground.
Figure 2
Click for Detail
Two sides are 2x12 and the other two are covered with 1/2" plywood. A 2x4 reinforces and stiffens the bottom edge of the plywood. This also make the base a little larger.
Figure 4
Click for Detail
It appears (see addendum) to be too tall for general work so it may be a light duty stand for close detail work. But you don't want to use this on soft ground or asphalt due to the lack of feet. It will end up embedded in either surface and leaning precariously.
Figure 5
Click for Detail
This stand has some handy and unique features.
There is a little built in container to catch punching "biscuits" that can be filled with water to cool them as they drop out. And the other end has a rack for hardies and other anvil tools.
I am not a proponent of steel stands but this one seemed to work well.
Figure 7
Click for Detail
But it is easy to take the same amount of lumber and make a very flimsy stand.
However, a springy steel stand or a flimsy wood stand that lets the anvil move around will reduce its efficiency a lot.
From Glenn Conner, maker of the stand in Figure 4 (My DO NOT example).
That stand is 1-1/2" x 1-1/2" x 1/4" angle iron for the legs and 2x3x1/4" angle iron for the box. It is 9x12 at the box and 18x18" at the floor.
Yes, I thought that it looked too tall also, but is about 24" at the box and 2" above knuckle high (on me) at the face. The original plan was to put an angle iron frame 6" off the bottom and a 1/4" plate steel shelf. Never got that far - yet. This is used outside on a creek gravel foundation and will only bury in about 1/2" at most.
The only differences I have found is that the ring of the anvil if best on wood. The wood stump (top photo) was great till the bugs found it. Tried everything I could think of to discourage them, but they are still there.
Both wood and angle iron are a solid base. The hammer works just a bit better on the angle iron. The angle iron is easier to move and setup.
Angle iron will reduce the ring considerably.
(Its the mounting, not the angle iron. -GURU)
Metal to metal contact between the anvil and angle iron was a concern so I put a piece of 1/2" wood (pine) between them. This seemed to cushion the anvil and adjust it to the stand. No more high spots to rock, or low spots that did not contact, again an improvement. think 1/4" or 1/8" wood would work even better. Nice imprint in the wood from the anvil last time I looked :)
Wrap it with chain, put a magnet under the heel and I have used the angle iron at 3 am without the neighbors being upset. On wood, the same anvil (without a muffler) can be heard at 4 city blocks during the summer.
Figure 8
Click for Detail
This anvil has a ring that will make your toes literally double over! After setting it into the form fit stand, the ring transferred down one of the legs!
Looking back the ring could have been reduced with a magnet on the leg.
Can't say enough about my enthusiasm for the concrete! Today I bent a 3/4 bending wench on a close bend using a fork placed in the anvil, didn't move the anvil around at all.
It's not my choice to endorse this anvil (you get what you pay for, and it is a serviceable anvil at a low price!)
Figure 9
Click for Detail
Pefect timing on the Anvil Stand tutorial!!
I built this one out of 2x12's from my scrap pile with no out of pocket expense :-) That's what I like! Now I'm building my gas forge stand out of an old grill.
Pierce Productions
Media Project Studio
Cincinnati, Ohio
Figure 12
Click for Detail
This is another 3 legged stand like Woody's and the Hoffi stand by Tom Clark. This one is a little fancier.
Legs are 2 x 2 sq. tube 1/8 - 3/16" wall Plate above legs 3/8" thick. Wood is 2 x 12 pine with pattern sections cut and added to hold anvil. Spikes are cut short and drilled and tapped at the bottom; bolts & washers hold spikes against the anvil. Surrounding kick plate is 10 gage.
Figure 13
Click for Detail
This stand is similar to Tom Clark's; I like it because I can work up very close to the anvil. Note (thanks to Paw-Paw): The hardie hole is open to the ground for an upsetting plate.
Figure 14
Click for Detail
I still personaly like a plain wooden stand but if you want a steel stand with tool holding capacity I really like the details of this one. The tool rack made of stove rack or barbeque grill, the Rail Road spike hold downs, tong rack. . . - guru
Figure 15
Click for Detail
I use in my workshop 3 different anvils. This one is very heavy and I do not use it every day. It stands away in my smithy. But it is bad idea to run with red hot iron in the workshop.
For moving this 200 kg (440 lbs) anvil I made stand on the wheels with a jackscrew. It is important to put rubber between the stand and anvil.
Best regards: Mart Salumaa www.hot.ee/theblacksmith/
Figure 16
Click for Detail
Delta TFS 100 pound anvil on stand.
Stand made from framing lumnber and 1/2" plywood with D-lugs to position anvil.
Figure 17
Click for Detail
This is a classic method of strapping an anvil down to a heavy wooden stump. It requires long bars threaded on the ends and designed to fit.
While the stand is smaller than the base of the anvil (it should not be) this was not uncommon in industrial shops. My large Kohlswa was attached to the end of a short section of riveted column with flanges smaller than the anvil base. It was strapped down with bent 1/2" square bar welded to the stand.
Figure 18
Click for Detail
This is an unusual wheeled stand with tool racks and handles. The total weight being about 300 pounds requires 150 pounds of lift on the handles. To be really easy and convienient I would make slip on handle extensions to make this easy to roll and control.
iForge is an Andrew Hooper Production
HTML Copyright © 2002-2010 Jock Dempsey, www.anvilfire.com
Email: webmaster